News
Specialize in research and development of polyoxymethylene (POM)/long fiber materials (PP.PA.TPU, etc.) in the fields of automobiles, electronic appliances, fasteners, sanitary ware, military industry, aerospace, ships, office supplies, agricultural irrigation, electronic appliances, etc.
Modified plastics 8 general direction
Release time:
2018-12-28 13:36
Source:
For plastic products in life, we only know that they are called plastics. What we don't know is that these plastics are also many different, some are brittle, and some are impact resistant. There are also many types of plastics. The pure resin properties of some polymers are not very good, and most of them cannot be used directly. They need to be modified to meet the needs of products. What do we often say about modified plastics? Generally modified plastics are modified density, transparency, hardness, processability, strength, toughness and so on.
Simply speaking, the modification of plastics is to change the original properties of plastics through some physical and chemical methods, increase or improve their original properties, and make them more suitable for terminal products. The following editors will introduce to you the 8 major directions of modified plastics.
1 density
There are two ways to change the density of plastics, one is to reduce the density of plastics, and the other is to increase the density of plastics, depending on the choice of terminal application. A common method to reduce the density of plastics is to add lightweight fillers or resins, but the density reduction is small; the other is foaming technology, which has a large weight loss range. But the difficulty is a bit more difficult.
2 Transparency
Regarding the transparency of plastics, the relationship between crystals and transparency is generally used. The transparency of plastics is related to the crystallinity of products. By controlling the different morphological structures of products, the transparency can be improved. To measure the transparency of a material, there are many performance indicators that need to be considered. Commonly used indicators are: light transmittance, haze, refractive index, birefringence and dispersion. A good transparency material requires excellent and balanced performance indicators.
3 Hardness and flexibility
hardness
Changing the hardness of plastics is divided into surface hardness and overall hardness. Generally, hard additives are added to plastics, which are generally rigid inorganic fillers.
Surface Hardness: Only improve the external hardness of plastic products, while the internal hardness of products remains unchanged. Low cost, mainly used for decorative materials, daily necessities, etc. The main methods are coating, plating and surface treatment.
Overall hardness: Generally, the method of blending plastics is improved by mixing low hardness resin with high hardness resin to increase its overall hardness. Common blend resins are: PS, PMMA, ABS and MF, etc. The resins that need to be modified are mainly PEs, PA, PTFE and PP.
Flexibility
Generally, plasticizers are added to change the flexibility of plastics. The main function of plasticizers is to improve the processability of resins, that is, to reduce the processing temperature and improve the processing fluidity. But adding it to related resins can also give products flexibility. Resins suitable for plasticizers to improve flexibility are: PVC, PVDC, CPE, SBS, PA, ABS, PVA and chlorinated polyether.
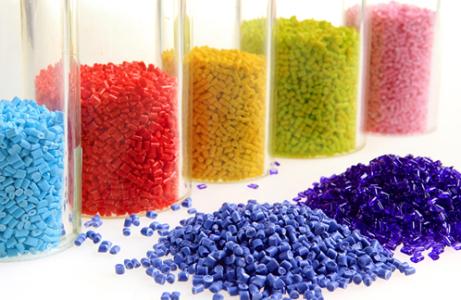
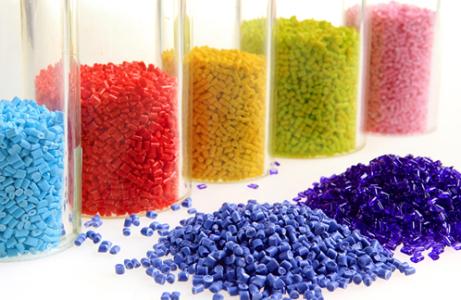
4 Processing performance
Improving the processing performance of plastics is generally manifested in: increasing the thermal decomposition temperature of the resin; lowering the melting temperature of the resin; improving the processing fluidity of the resin; and improving the melt characteristics of the resin. The commonly used modification method is to add modification, add plasticizer and lubricant. Plasticizer can improve the plasticity of the polymer; the role of the lubricant is to reduce the friction between the material and the surface of the material and processing equipment, reduce the flow resistance of the melt from the surface, reduce the viscosity of the melt, improve the fluidity of the melt, avoid The adhesion of the melt to the equipment improves the surface finish of the product.
5 intensity
The reinforcement of plastics is generally the addition of reinforcing fillers and fibers. Most conventional fillers are added directly to the resin, which will cause the tensile strength of the plastic to decrease. However, some special fillers added directly will not only cause a decrease in tensile strength, but will increase the tensile strength to a certain extent. We call this type of filler a reinforcing filler. The reinforcement modification of reinforcement is far less than that of reinforcement fiber, and it can only be used in occasions where the strength requirement is not too high. Plastic fiber-reinforced methods are commonly used and effective reinforcement methods.
Reinforced fiber materials are the main reinforcing materials for plastics, and their dosage can account for more than 90% of the entire reinforcing materials. It mainly includes two categories of fibers and whiskers. The specific varieties are: inorganic (such as glass fiber, asbestos fiber, carbon fiber, whisker, quartz fiber, graphite fiber and ceramic fiber, etc.), organic (such as PAN fiber, polyethylene Fiber, PA fiber, PC fiber, PVC fiber and polyester fiber, etc.), metals (such as boron fiber and metal whiskers such as aluminum, titanium, calcium, etc.).
6 toughness
The toughening of plastics is generally blended with elastomer materials, which enhances the toughness of plastics. Commonly used elastomer toughening materials are: high-impact resins, such as CPE, MBS, EVA, modified petroleum resin (MPR), etc .; high-impact rubbers, such as ethylene propylene rubber (EPR), EPDM (EPDM) , NBR, styrene-butadiene rubber, natural rubber, butadiene rubber, neoprene, etc.
7 Thermal performance
The thermal properties that affect the use of plastic products are mainly heat resistance temperature and low temperature resistance. The heat-resistant temperature can be expressed mainly by heat deformation temperature, Martin heat-resistant temperature and Vicat softening point; the low-temperature resistance temperature can generally be expressed by embrittlement temperature.
In all fillers, except for organic fillers, most inorganic mineral fillers can significantly increase the heat-resistant temperature of plastics. Commonly used heat-resistant fillers are: calcium carbonate, talc, wollastonite, mica, calcined clay, bauxite and asbestos.
In addition, the plastic's effect of changing the heat resistance is better than that of filling, mainly because the heat resistance temperature of most fibers is very high, and the melting point is more than 1500 degrees Celsius. Commonly used heat-resistant fibers are: asbestos fibers, glass fibers, carbon fibers, whiskers, polyamide fibers and acrylic fibers.
Previous Page